Bench tests for new digital functionalities may be fully automated thanks to a new Porsche Engineering concept. The processes that go along with the testing are likewise automated through continuous integration. As a result, functional testing for Porsche Connect services is more effective.
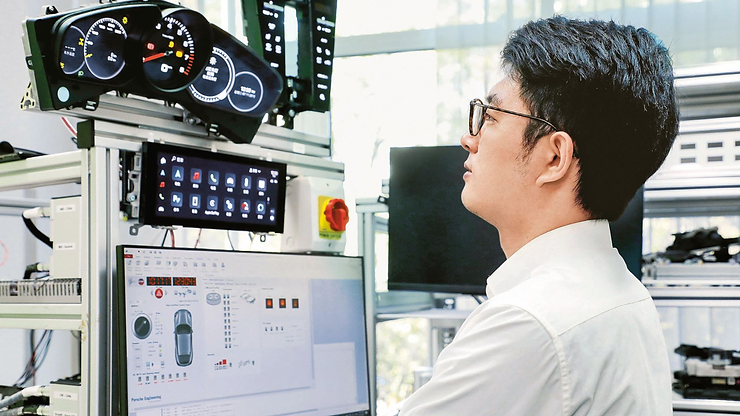
The digital services of Porsche Connect make it possible to easily upgrade the equipment in a Porsche and add optional capabilities. Drivers now have access to a variety of extra features that help them before, during, and after their trip. Drivers may simply add features like active lane guiding or an intelligent management function that changes the climate and speed settings based on the amount of charge left in the electric vehicle, for example, to make driving even safer. An international test team of about 110 employees at Porsche Engineering verifies the software for all Porsche model lines and individual models before it enters the vehicle to make sure that the features are smoothly integrated into the vehicle system and that the numerous different services work together without any issues.
The integration of many software worlds—automotive, infrastructure, and smartphone—creates a particularly complicated ecosystem for current connection solutions like Porsche Connect. In addition, there are numerous distinct software tasks that must be evaluated in all possible configurations, as Dr. Fabian Hinder, a project engineer specialist at Porsche Engineering, explains.

The intense testing process ensures that the integration of new features into the vehicle system proceeds smoothly.
The software must thus go through all the required test procedures in the lab and on the road, which are just as rigorous as you would anticipate. At its facilities in Shanghai, Cluj, Prague, Ostrava, and Weissach, Porsche Engineering has built up 30 unique HiL (hardware-in-the-loop) test benches for bench testing Porsche Connect services. The remaining car systems are simulated in a virtual, real-time environment; only the four core control units installed in the vehicle for the Porsche Connect services are integrated as hardware. "This residual bus simulation, as it is known, is primarily used to generate the communication data for the various bus systems, meaning that we can test the Porsche Connect services under realistic conditions on the test bench," explains Daniel Klauber, a development engineer at Porsche Engineering.
Modern networking technologies create a particularly complicated ecology due to the integration of several software realms.
Dr. Fabian Hinder is a Porsche Engineering project engineer specialist.
It is tested to see if the program responds to various simulation-generated conditions as expected. According to Klauber, "the experts at Porsche Engineering decide how the further test sequences should be arranged based on the outcomes of these basic functional tests, known as smoke tests. To test market-specific features, these tests are carried out globally in various locales.
Despite the fact that the residual bus simulation and the execution of the HiL test have long been largely automated, the setup of the test bench and the processing of the test's results have typically been done by hand. For instance, in order to install the most recent version of Connect software onto the control units in the test environment, the test bench engineers had to manually choose it from the data management system.
Complete Automation
The test bench tests are now completely automated thanks to a new Porsche Engineering concept. Not just the tests themselves but also the supporting procedures are automated. The system uploads the software to the test control units and independently administers it for the Connect services. Automation is also used for the control unit parameterization and the beginning, running, and analysis of bench tests.
"Since there is no need to perform manual chores in between process phases, this lessens the workload of the test engineers and speeds up the tests. This results in a 90% reduction in the amount of time needed to manually set up the test benches. The technology also actively informs the test team of key test findings. As a result, the team can entirely focus on error analysis, according to Hinder.
Interdisciplinary Team
Additionally, some test bench tasks no longer require substantial specialist knowledge, as was the case, for instance, when new software had to be manually updated onto test control units. "In the Connect environment, there is an incredibly high variance because there are so many services, markets, and car model lines to serve. The HiL test bench must be fully automated in order to cover these variances with tests when there are weekly software deliveries, according to Carsten Weigt, Team Lead Shared Test & Integration at Porsche AG.
Using internal expertise, a multidisciplinary project team at Porsche Engineering enabled complete automation. At numerous places throughout the world, specialists in software development, process automation, test automation, residual bus simulation, and test infrastructure design collaborated. The team's effort included adding interfaces it had created on its own to the building blocks already in place to enable a more comprehensive automation of the process chain.
“It is imperative that the HiL test bench be fully automated.”
Carsten Weigt Team Lead Shared Test & Integration at Porsche AG
David Karimi, a development engineer at Porsche Engineering, adds, "To reduce complexity, we built automatic routines that make it easier for us to activate activities. The specialists made up for any shortage of full-automation building blocks using internal advancements.
This made it possible to develop tools like a software crawler that downloads software from providers' servers automatically and a local client for managing test benches, for example. Other examples include tools for reporting all outcomes of the many automated process steps as well as generic control logic.
Modular Design
Continuous integration is another name for the approach taken to fully automate the test benches. The methodology's foundation is the open-source Jenkins software system, which enables continuous assembly of software parts to create an application. Porsche Connect services are still being rapidly and dynamically developed. We pushed on with the implementation of HiL automation in order to be able to safeguard the new services and changes in good time, despite the rate of development. With continuous integration, we are now able to flash and code the control units quickly and automatically download updated control unit software, according to Porsche AG's Dickson Ng, Product Owner Automation Platform & Continuous Integration.

Because multiple modules can be combined into a new overall process based on the use case, the continuous integration technique gives a high degree of flexibility for modifications and extensions. Because of this, Hinder claims that "our approach is suitable for automating all bench tests for all domains. "The first requests from other departments have already been made. The project team is currently concentrating on integrating complete automation into all Connect HiL test rigs from Porsche Engineering globally. All other test rigs in Germany, China, and the Czech Republic are now to be retrofitted following the initial implementation's success. By the end of 2023, all HiL test rigs for Porsche Connect services are anticipated to be totally automated.